
This is a reminder that fundamentally, mechanistic-empirical design is an iterative process. It is also important to tackle the second question even if the initial design assumptions appear satisfactory. If it is not acceptable, the design process will obviously need to move on and consider alternatives.
#Pavement design software globally trial#
If the trial design is acceptable, it should be retained as an option for the final pavement design. Or, it may be a matter of whether, in the judgment of the design engineer, the predicted level of performance is acceptable.

The agency that owns the pavement will typically have specified criteria that can be used to answer the first question. The first question can be stated as, “Does the predicted performance of the pavement satisfy criteria for the design, such as the desired service life of the pavement, based on the level of distress and potential maintenance and rehabilitation needs?” The second question is, “Are there reasonable alternatives to the initial design assumptions that could generate better predicted performance or lower life cycle costs?” Both traffic and climate are used as inputs in the MEPDG process.Īt this point, there are two design questions that need to be considered.
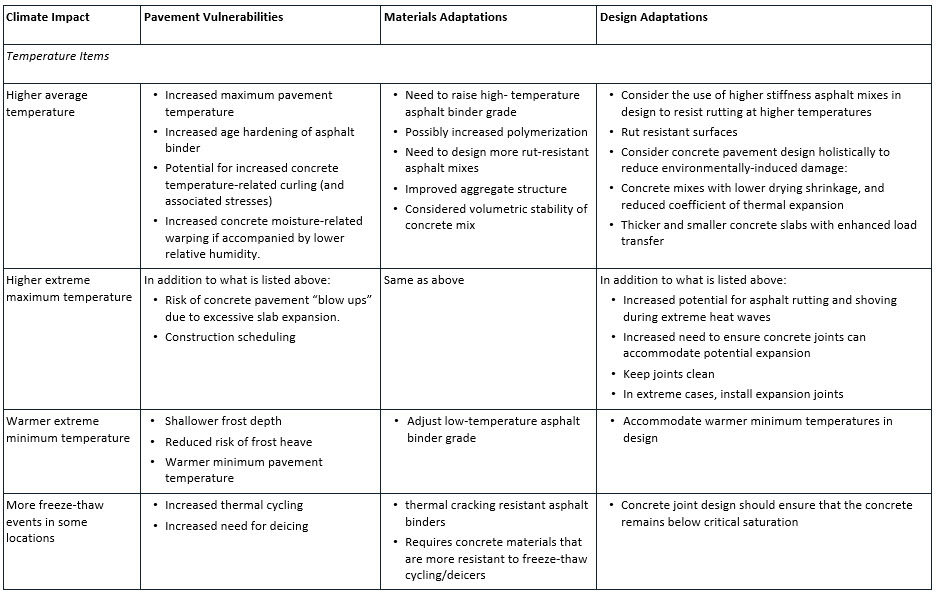
This leads to an estimate of the level of damage the pavement will sustain over time, in terms of pavement distresses and deterioration in ride quality. MEPDG software can compute how the trial design will respond to the load and environmental stresses created by these inputs. In mechanistic-empirical design, the design of the pavement structure is initially assumed on a trial basis, along with inputs for traffic and climate. In conventional design methods, various inputs are considered and used to produce the design requirements for the pavement structure. One of the significant changes with the MEPDG is that the approach to pavement design is effectively reversed. In conjunction with the MEPDG research project, software was also developed to assist in organizing and performing these design calculations. By using newer data collected as part of the Long-Term Pavement Performance (LTPP) program, the MEPDG allows for design inferences that would be harder to justify from the limited designs and traffic levels covered by the Road Test.
#Pavement design software globally update#
Recognizing the importance of local calibration, this report discusses the general approach to local calibration undertaken for state agencies for asphalt concrete pavements, followed by results of the local calibration efforts and where possible, the recommendations for implementing the globally or locally calibrated models.The MEPDG is designed to update the 1993 AASHTO Guide for Design of Pavement Structures, which is primarily based on empirical observations from the AASHO Road Test that began in the 1950s. Without properly conducted local calibration efforts, the implementation of MEPDG will not improve the pavement design process and may yield errors in predicted thickness of asphalt pavements. Therefore, local calibration studies should be conducted to address these differences and to adjust, if necessary, local calibration coefficients of the transfer functions used to predict pavement performance in the Pavement ME Design software to better reflect actual performance.


It is expected that such parameters would affect field performance. While the resulting performance models are representative of national-level conditions, they do not necessarily represent construction and material specifications, pavement preservation and maintenance practices, and materials specific to each state. The MEPDG was nationally calibrated using Long-term Pavement Performance (LTPP) program pavement sections as a representative database of pavement test sites across North America. It then utilizes the cumulative damage in transfer functions to "empirically" predict pavement distresses for each trial pavement structure. In flexible pavement design, the software "mechanistically" calculates pavement responses (stresses and strains) based on the inputs and trial design information and uses those responses to compute incremental damage over time. Many state highway agencies have considered adopting the Mechanistic-Empirical Pavement Design Guide (MEPDG) and the accompanying AASHTOWare Pavement ME Design software to supplement or replace the empirical American Association of State Highway and Transportation Officials (AASHTO) Pavement Design Guides and the widely used DARWin pavement design software. Pavement ME Design – A Summary of Local Calibration Efforts for Flexible Pavements
